Successful Results
Location: Leeds, UK
Sensor data is reliable and accurate and transmits data without interruption. The vertical displacement of masonry arch relative to stone spandrel is similar in magnitude, allowing this to be used to monitor overall displacement. Engineers are able to determine the overall structural integrity of the bridge using remote condition monitoring system and ensure safety to its users without having to implement disruptive road closures. Trends in dynamic behaviour of the bridge can be assessed in the long term to determine degradation.
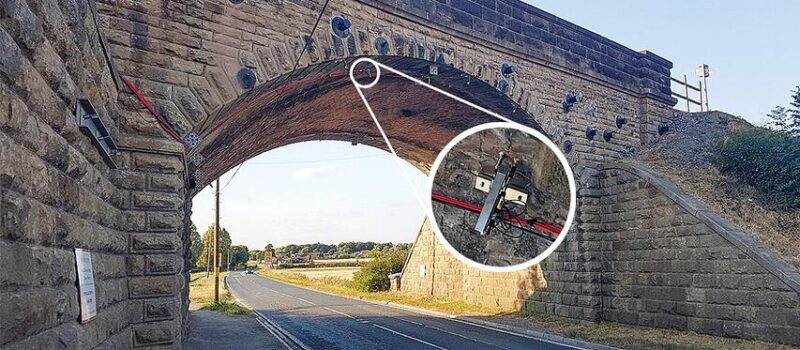
Background
Network Rail’s asset engineers are responsible for maintaining a large number of ageing structures that form part of the UK’s railway infrastructure. Network Rail has traditionally used deflection monitoring of vertical crown displacements at the arch soffit to assess the condition of structures. This approach uses a telescopic pole equipped with a displacement sensor, but proves impractical in many cases where structures overly active highways or watercourses. As a result, a study was commissioned by Network Rail to evaluate the potential monitoring technologies that could be employed on their masonry arch structures. A 150-year-old single-span masonry arch bridge was selected for trials. The structure carries two tracks and serves as a main rail artery in the Northern UK. It is used by several hundred passenger trains on a daily basis as well as occasional freight trains.
Scope/Objective
The bridge shows signs of past damage from its 150-year working life, including spandrel separation cracks, longitudinal cracking to the southeast of the arch barrel, and bulging of the spandrels, parapets and wing walls. Network rail is required to periodically monitor the structure, despite recent works being carried out to stabilise the structure using tie bars, stitching, and grouting of cracks. Their asset engineers were keen to explore the range of alternatives available and determine whether these could improve on the conventional displacement monitoring that was being carried out previously.
If successful, the monitoring system developed for this bridge would be adapted to multiple other “at risk” structures which were exhibiting similar defects due to their age.
Challenges
Measurements needed to be taken before/during/after the trains crossed the bridge to determine if the trains caused stress, due to their loads.
A long term reporting solution for how much the cracks were expanding/contracting was also required, along with the overall need for continuous sensor data input (over 100 samples per second, per sensor) on a battery system – AC power was not an option.
Solution
RST provided a combination of instrumentation with data logging for real time alerting as well as dynamic data while the train was crossing. Crack Meters were installed to monitor the expansion/contraction of the cracks and Strain Gauges were used to determine the stress due to the load of passing trains at different locations. A solar panel system was configured to provide 100% active data acquisition.
Benefits
- The customized automatic data transfer system allowed the bridge to remain open during the entire process – disruptive road closures with a 38-mile diversionary route were minimized.
- Deflections monitored under load of >35,000 trains (August 2018- March 2019).
- RST’s Field Services Team provided technical services for installation and support for configuring the data logger and setting up the analysis software.
- Afterward, RST also provided assistance in developing scripts to process data.
- Quick installation – installed over the course of only 2 days.